…but the truth remains that I love the “doing” of things more than the “writing about the doing” of things. Thus I have been remiss in posting. Alas.
I have been hard at work on my breed study, though, so let’s jump right in. If you follow me on Instagram (@thehopefulfleece)* you know that I recently happened upon Jillian Moreno’s Instagram post about steaming commercial top to revive the crimp. Whaaaat? I had to try it right away.
I put a little pot of water on to boil, and slowly moved half of my 1 oz. Perendale sample back and forth over the steam, allowing it to get damp. (I also touched this sample to the pot a couple of times – don’t do this. It singes the fiber.) Lo, look what happens! It crimps and puffs right up!
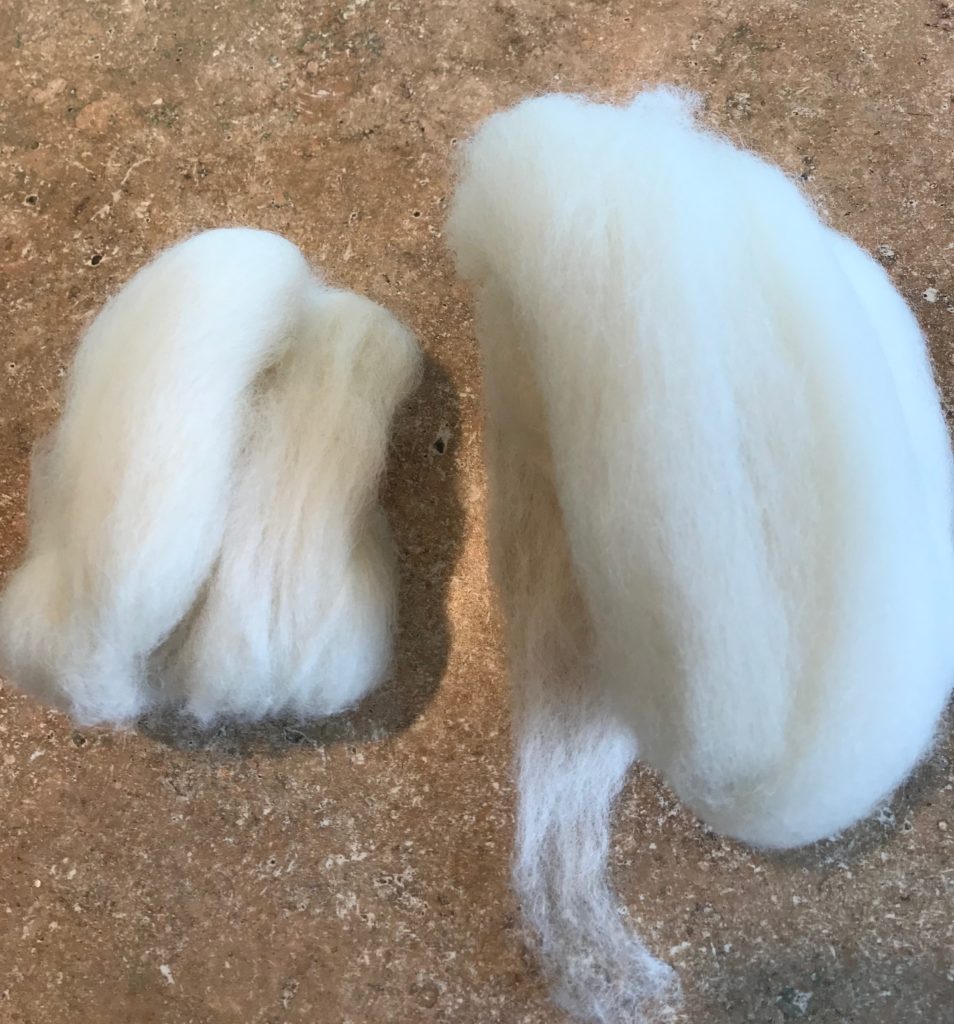
I used this re-crimped sample to make the rolags for semi-woollen spinning on my blending board, and lemme tell you, it’s a game changer. It made the process of making the rolags much easier since the fibers were looser, and it also made a huge difference in terms of how the fibers drafted for long-draw spinning. I prepared half my top in this way for all four of the samples mentioned here, and will do this for the rest of my breed study samples. I only wish I’d known about it sooner!
Perendale
Perendale is a cross between Romney and Cheviot. I did notice that the fiber felt a little “crispy” – it was similar to the Cheviot in that way. As you can see above, the Perendale fluffed up quite a lot upon steaming, and the resulting semi-woollen yarn was light, airy, and appropriately fuzzy. This fiber drafted like a dream using both the supported long draw and short forward draw, and overall was extremely pleasant to spin. The semi-woollen yarn is softer, but the semi-worsted retains more luster.
However you choose to work with this fiber, I think you will love the result. It may not be next-to-skin soft for most people, but it would make lovely outerwear, socks, and maybe even a hat.
Texel
I was at the Fat Lamb Fiber Festival in Scio, OR recently when I saw these adorable little guys:
I couldn’t find the girl they belonged to, but after seeing some Texel fleeces in the fleece show, consulting my Field Guide to Fleece, and doing a little recon on Instagram** to see if anyone from the festival could confirm, I discovered that they are indeed Texel lambs. How cute are they? Clearly I had to spin my Texel sample next.
Again, steaming the top made a huge difference in terms of texture. Texels were created by cross-breeding a native sheep of the Netherlands with Leicester and Lincoln Longwools, with the desired result of a high quality meat sheep. The bonus for spinners is that their fleece is great too! My Texel sample is a little on the yellow side – at least when you compare it with the other breeds sampled here – but it is not displeasing. It’s just a bit creamy.
All that air in the fiber I carded into the rolags made an extremely fluffy semi-woollen yarn – so much so that it ended up bulky weight! It knitted up into a surprisingly soft swatch, and I suspect it would be very warm as a cardigan or hat.
The semi-worsted sample spun up at worsted weight, and was much smoother than the semi-woollen sample. Spun finer than I did it might be an interesting match for a lace pattern – I do love a “rustic” yarn in lace or cables.
I really enjoyed working with this fiber – I found it to be very easy to spin and nice to knit. I would be interested in spinning it from the fleece sometime!
Romney (Kent Romney, Romney Marsh)
Romney was actually the wool that my spinning teacher put into my hands for my first lesson – and I suspect it may also have been what I used to learn on a spindle several years ago. Romney is in the longwool family, but is considerably softer than some of its longwool counterparts. This is part of why it’s often used as a “beginner fiber” – it is sturdy, crimpy, and easy to spin. Its longwool heritage brings a wonderful luster, and it can be used for a multitude of garments and household items, depending on the fineness of the particular fleece you’re working with.
Even though I steamed half of this sample, I found that the difference between the semi-worsted and semi-woollen samples was more subtle than I have seen with some other wools I’ve worked with for this study. It is easier to feel the difference than to see it – and it’s a little more visible in the knitted samples than in the skeins. Possibly it’s more visible just because my spinning is less consistent in the semi-woollen sample. Oh well.
My takeaway from sampling this Romney is that I totally underestimated it when I was a beginning spinner. It is a really nice, versatile wool. The luster adds interest, and it’s really just lovely to use. I hear it also takes dye well, but that’s an experiment for another day. Oh, and I want to spin enough to make a pair of mittens. Romney just screams “cozy mittens” to me.
Polwarth
And now, after a medium-textured wool frenzy…something completely different. Polwarth is a finewool, found only in Australia, and it is a cross between Merino and Lincoln Longwool. I only have one word to describe Polwarth, and that’s dreamy.
I worked with some Polwarth shortly after I learned to spin, and at that time I found it to be really challenging. What I didn’t know then is that really, all the finewools are harder to spin than something with more substance. As I recall, I liked Polwarth better than Merino, though, and that’s partly because of the length of the fibers. The longwool influence helps a lot with that.
I have a little more experience now, and I found that this sample was a joy to work with. Again, I was surprised that the semi-woollen and semi-worsted samples were so similar. There is more loft to the semi-woollen sample, but it’s easier to feel than to see. Both samples retained their luster, and the individual fibers stayed pretty smooth even in the semi-woollen sample. Both skeins have a significant “squish” factor, and they are soft as can be.
Polwarth is next-to-skin soft in every way. There are no poky ends to contribute to the prickle factor, and both swatches are smooth and comfy. The thing I haven’t tested is pilling – it might pill quickly, but I suspect that the length of the staples will help prevent that, even in a woollen-spun yarn. I might have to knit another swatch and rough it up.
In the end, I am totally in love with Polwarth…and I still like spinning it more than I like spinning Merino. If you have someone in your life who says they can’t wear wool – try Polwarth. It just might change their minds.
*And honestly, if you don’t follow me on Instagram you should start. I’m WAY more reliable about posting there.
** See? WAY more reliable.